UNDGÅ DENNE FEJL NÅR DU AUTOMATISERER LAGERET
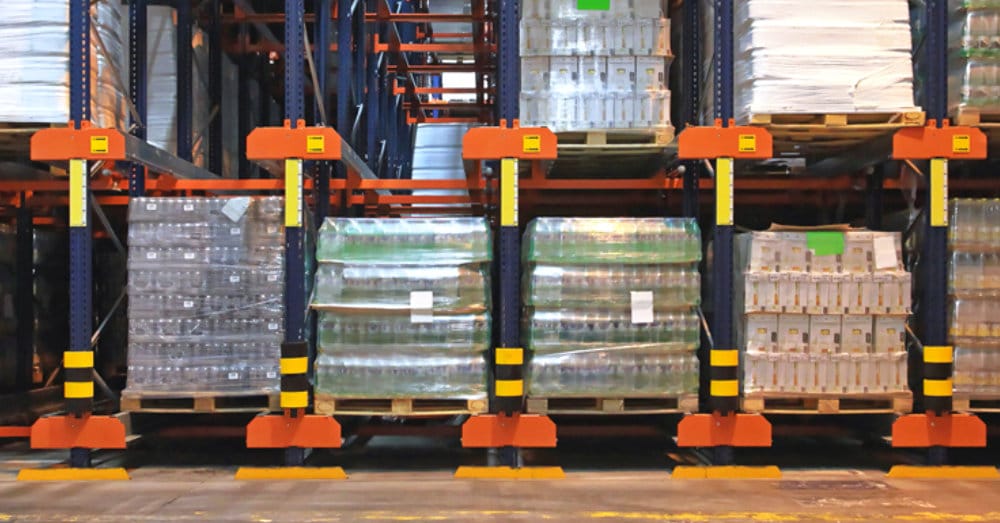
“Amazon kommer!” Alle råber disse ord for tiden, og lagerchefer bliver bombarderet med krav om automatisering af lageret. Hvis du også overvejer at investere i automatisering, kan du lære meget af denne fejl, som en lagerchef begik, da han investerede i lagerautomater.
På de nordiske markeder er lagerets kvadratmeterpris høj. I hvert fald højere end andre steder i verden. Derfor er der også fokus på én særlig vigtig ting: At udnytte pladsen maksimalt.
Med lagerautomater kan du udnytte pladsen på en helt ny måde – i højden, men også i organiseringen, da automaten kan operere effektivt med varer på en anden måde end de almindelige lagerhylder. Det kan derfor være en god investering, når du er ved at nå grænsen for din lagerkapacitet.
– Og dén grænse nåede en lagerchef, som vi kender og ofte sparrer med i udviklingen af vores WMS til lagerstyring. Han investerede derfor for noget tid siden i sine første to lagerautomat.
Vi har fået lov at viderebringe hans indledende erfaringer med automatisering af lageret, fordi der er god læring i dem for dig, der også overvejer at investere i lagerautomater.
Du får her et indblik i forløbet.
Når automaten fungerer, men fyldningsgraden falder – hvad går der så galt?
Vi møder lagerchefen efter, at han har indkøbt sine lagerautomater.
Leverandøren havde gjort et godt stykke arbejde. For implementeringsprocessen var gået rimelig smertefrit, automaten kom hurtigt op at køre, og resultatet var som forventet: Der blev frigivet mere plads på det manuelle lager.
Succes!
Desværre stopper historien ikke her.
Lagerautomaterne kørte ganske vist upåklageligt, men alt for hurtigt begyndte lagerets fyldningsgrad igen at falde, og lagerchefen stod med et nyt dilemma. Skulle han indkøbe endnu en automat?
Vi tog et kig på logistikken sammen – og konklusionen blev hurtigt et rungende nej!
Ikke fordi, der var noget galt med automaten eller hans investering i den. Men fordi, der var en meget væsentlig fejl i den overordnede logistik, som han fuldstændig havde overset, og som heller ikke var automatleverandørens fokus under implementeringsprocessen.
Fejlen lå i samspillet mellem det manuelle lager og automaten.
Ser du. Med den slags lagerautomater medfølger jo et styresystem forkortet PLC. Det styrer grundlæggende kommunikationen i og omkring automaten, når plukkeren fremsøger varer.
Men PLC-styringen tager ikke højde for arbejdsprocesserne på det manuelle lager.
Derfor kørte det manuelle lager og lagerautomaterne fuldstændigt hver for sig.
Det betød i dette tilfælde, at de varer, der skulle ind i automaten, langsomt begyndte at finde vej tilbage på det manuelle lager. Fyldningsgraden i automaten faldt, den begyndte at miste sin værdi, og lagerkapaciteten som helhed led igen under det.
Det var blot ikke synligt for lagerchefen, fordi der ikke var en samlet styring mellem automaten og arbejdsprocesserne på det manuelle lager.
At investere i endnu en automat ville ikke løse dette grundlæggende problem.
Hvad skulle lagerchefen have gjort i stedet?
Historien kan i sin enkelthed lyde ret banal. I virkeligheden er det helt modsat.
For lagerautomatisering – uanset om der er tale om en automat eller ej – er ret kompleks. Risikoen for at overse noget i samspillet mellem automatiseringen og de mennesker, der til dagligt arbejder på lageret, er i høj grad til stede.
Det kan gøre, at du ikke får det fulde udbytte af din investering i automatisering
– uden, at du opdager det.
Derfor er det væsentligt at få en samlet styring på plads fra starten. Og dét havde vores lagerchef ikke.
Alle råbte: “Amazon kommer!” efter ham. Han var gennem længere tid blevet bombarderet med krav om automatisering af lageret. Da det rigtige tilbud kom, slog han til.
– Det er der absolut intet galt i.
Implementeringsfasen manglede blot et vigtigt skridt: En samlet styring mellem automaten i form af PLC-systemet og den daglige koordinering af opgaver med lagermedarbejderne.
Derfor hjalp vi ham med at koble automaten til vores WMS via en nem integration mellem WMS og PLC, og herfra kørte arbejdsprocessen således:
- WMS sender via en skanner besked til lagermedarbejderen om, at der skal plukkes en eller flere varer i automaten.
- WMS sender samtidigt besked til PLC (automaten) om, at en mand kommer for at plukke vare A og B.
- PLC (automaten) kører med det samme hylden med vare A frem og gør klar til at køre hylden med vare B frem umiddelbart efter. På den måde optimeres plukket.
- Lagermedarbejderen foretager plukarbejdet og noterer det på skanneren.
- WMS holder styr på automatens varebeholdning, ligesom den holder styr på det manuelle lagers varebeholdning, og som en integreret del af lagerarbejdet allokerer WMS automatisk et opfyldningsjob til en lagermedarbejder, hvis automaten skal fyldes op.
På den måde kan lagerchefen nu sikre, at der hele tiden er styring med både indlagring og pluk, uanset om det er mennesker eller maskiner, der udfører arbejdet.
Det betyder selvfølgelig ikke, at han aldrig igen vil opleve, at fyldningsgraden falder. Til gengæld vil han ikke være i tvivl om, hvor han skal gribe ind. For det vil data fortælle ham.
Om han skal investere i en automat ekstra, bygge lageret ud, blot foretage en oprydning, eller om lagerkapaciteten har nået sit maks, og der er tale om et behov for en kombination af tiltag.
Den slags giver ro i maven.